Self-drilling anchor bolts are an efficient and convenient geotechnical support material widely used in projects such as tunnels, slopes, and foundation pits. However, in actual construction and use, connection failures between the coupler and the hollow anchor bar frequently occur. This issue not only impacts project progress and quality but may also pose serious safety risks. So, what exactly causes this connection failure? Is it a material issue, a design flaw, or improper construction? This article will explore the common causes of connection failure in self-drilling anchor bolts and provide effective solutions and preventive measures.
Structure of the Self-Drilling Anchor Bolt
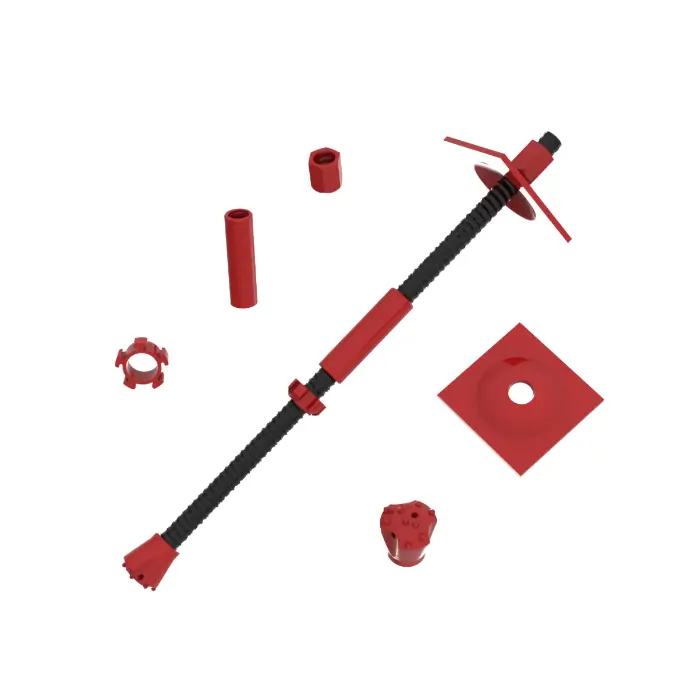
The self-drilling anchor bolt consists of six components: the hollow anchor bar, drill bit, coupler, plate, nut, and centralizer.
- The hollow anchor bar is made of high-tensile alloy steel seamless pipe, which meets various complex geological conditions with its tensile and yield strength as per design requirements.
- The drill bit is made of wear-resistant metal and includes slurry discharge holes.
- The coupler is a rod extension component that ensures an equal-strength connection with the hollow anchor bar.
- The plate is installed at the end of the anchor bar, positioned between the nut and the rock layer.
- The nut is a device with internal threads that transfer the anchoring force of the hollow anchor bar to the plate, locking it in place.
- The centralizer ensures that the hollow anchor bar remains centered in the hole. It is installed on the hollow anchor bar, positioned in front of the coupler, and ensures the rod is aligned.
Working Principle of Self-Drilling Anchor Bolts
Self-drilling anchor bolts can be used in slope engineering, foundation and base engineering, tunnels, and underground works. The construction method and working principle vary depending on the application scenario.
- Slope Protection: The self-drilling anchor bolt is drilled into the slope body at a certain angle using a self-drilling anchor bolt drill. After drilling, grout is injected through the hollow channel inside the rod. The grout fills the rock and soil fissures from the drill bit’s slurry discharge holes and tightly wraps around the rod. After drilling and grouting, the plate and nut are installed against the rock surface, and once the grout sets, it forms an anchoring body with the anchor rod. When the rock or soil deforms, the force applied to the plate and nut is transferred to the anchoring body, which, through friction with the rock or soil, provides anchoring force and effectively prevents slope collapse.
- Foundation Pit Protection: The self-drilling anchor bolt uses a hollow anchor bar with external threads as a drilling rod, with a drill bit installed at the end of the rod. The rod is driven into the strata using a drilling machine, and grout is injected through the hollow core to surround the rod with cement grout or pure cement slurry. It forms a bond with the surrounding soil, producing anchoring effects. When the soil deforms, the frictional force at the contact surface between the rod and the soil creates passive stress on the rod, mainly applying tensile force to stabilize and reinforce the soil.
- Tunnel Forepoling Support: Umbrella steel pipe roofing solves the problem of hole collapse, drill jamming, and the inability to insert ordinary flower tube pipe sheds after drilling in IV or V-grade surrounding rock conditions. Umbrella steel pipe roofings are highly flexible, cause minimal radial plastic deformation of the surrounding rock, and form a bearing arch after installation. It enhances the support effect and ensures the safety of tunnel excavation and initial support. Compared with traditional pipe shed support construction, the umbrella steel pipe roofing construction completes drilling and grouting in one step, significantly improving construction efficiency and reducing surface settlement while preventing surrounding rock collapse.
Common Manifestations of Connection Failure
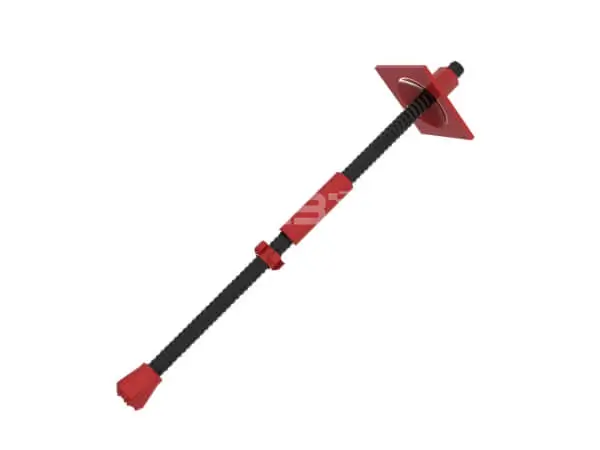
Connection failure manifests as thread disengagement, coupler expansion, or necking in the hollow anchor bar. These issues prevent the anchor rod from transmitting loads properly and may even cause the loss of support functionality.
Main Causes of Connection Failure
- Stress Concentration Under Axial Tensile Load: Under axial tensile load, stress concentration occurs at the threaded connection between the coupler and the hollow anchor bar. As the load increases, the stress concentration becomes more significant, eventually leading to thread disengagement.
- Radial Deformation Mismatch: During axial tension, the coupler, and the hollow anchor bar experience radial deformation. The coupler may expand outward, while the hollow anchor bar may experience “necking.” This mismatch in radial deformation reduces the contact area between the internal and external threads, leading to disengagement.
- Plastic Deformation of Materials: When the load exceeds the material’s yield strength, the coupler and the hollow anchor bar undergo plastic deformation. This irreversible deformation causes thread compression and flattening, increasing the risk of connection failure.
- Unreasonable Thread Structure Design: Self-drilling anchor bolts use R-type threaded tools, which differ significantly from ordinary threads. If the thread design is flawed or lacks precision in machining, it can affect the stability and reliability of the connection.
How to Prevent Connection Failure
- Optimize Thread Design: Optimizing the thread structure to increase the contact area and the interlocking threads significantly enhances the connection’s stability and strength.
- Enhance Material Strength: Choosing high-strength and high-toughness materials for the coupler and hollow anchor bar can effectively resist plastic deformation and prolong service life.
- Strict Control of Processing Precision: Ensure the precision and consistency of thread processing to avoid connection failure caused by machining errors.
- Strengthen Construction Monitoring: During construction, continuously monitor the forces and deformation states on the anchor rods to promptly identify and address potential issues.
In conclusion, the connection failure between the SDA bolt coupler and the hollow anchor bar is a complex problem involving multiple factors, including materials, design, and construction. By analyzing the causes of failure and implementing preventive measures, we can effectively improve the reliability and stability of the connection, ensuring the project’s safety and quality.